The Anaerobic Pasteurizing Conditioning APC System is employed worldwide in the compound feed and related industries for the long term conditioning and processing of grains, legumes, soya and mixed feeds prior to pelleting or cooling processes. Additionally, it is used to condition and process whole grains and legumes prior to flaking.
The APC System is composed of:
- Vaporator Direct-Fired Steam Generator
- VAPORENERGY Vertical Conditioner"
- PLC or Process Controller based Control System
The APC System offers:
- Increased Pellet / Flake Quality
- Increased Feed Conversion
- Elimination of E-Coli and Salmonella
- Fuel Savins of 30 - 40%
- Best Time, Temperature and Moisture Control
The vertical flow of moisture and temperature-regulated steam is counterflow to the meal or whole grain moss, which is fluidized by the arrangement of the rotor blades and steam injection in the lower section. Controlling the steam's moisture level and the product column's dynamics, each particle contacts counterflowing steam and inert gases. Complete conditioning is thus assured for a predetermined amount of time. In most cases, a four-minote conditioner residence time provides enhanced qualities of postconditioning processes such as pelleting or flaking.
This full particle treatment yields a higher level of gelatinized starches, sugars and proteins while absorbing other feed ingredients such as fats, molasses, vitamins, enzymes and more.
The conditioned particle enters the pelleting press or flaking mill with less friction and significantly higher outputs than unconditioned particles. Motor loads are reduced. Well pocked pellet or flake structures yield improved abrasion and durability characteristics.
The anaerobic environment (approximately 4% oxygen) suffocates aerobic bacteria while the long-term conditioning pasteurizes each particle at controlled moisture and temperature levels. Continuous input of cool meal or groin to the upper section of the material column allows for optimum energy scrubbing, keeping exhaust temperatures well below conditioning temperatures. Feed ingredients condense in the cooler moss and are not lost to ambient.
VAPORATOR 98% Efficient Direct-Fired Steam Generator can instantly produce anaerobic (oxygen deficient) steam with independently variable heat, moisture content and volume. Vaporotor systems operate at very law pressure ( < 1 bar}; eliminating the need for a boiler operator and saves 30-40% of the fuel costs. |
|
Conditioner Dynamics |
 |
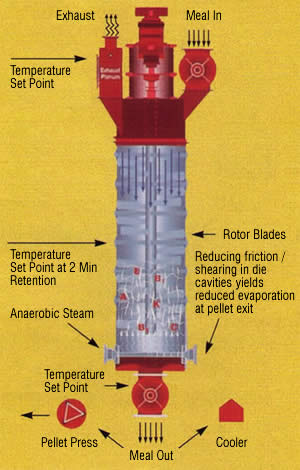 |
 |
Cold Exhaust
|
Steam, containing feed additives, condenses in lower temperature meal and is retained in falling meal.
Gelatinization, increased plasticity, and reduced evaporation results in tight packaging of feed additives and improved pellet quality.
Vapor is anaerobic to eliminate E-coli and Salmonella. |
Conditioned Feed |
|
|
 |
 |
|
Cold Meal
Warms Slowly
|
Meal reaches higher temperature. Feed additives are mixed. The approximate moisture of meal is 12-14%. Pasteurization begins.
Meal reaches set temperature. Gelatinization of starch begins; feed additives permeate into softened particles. Approximate moisture of meal is 14-16%.
Pressure in lower region forces additives into softened particles. Gelatinization continues and particle plasticity occures yielding reduced friction at die/rolls; E-Coli, Salmonella eliminated! |
Anaerobic Steam |
|
 |
|
|
|
|
|